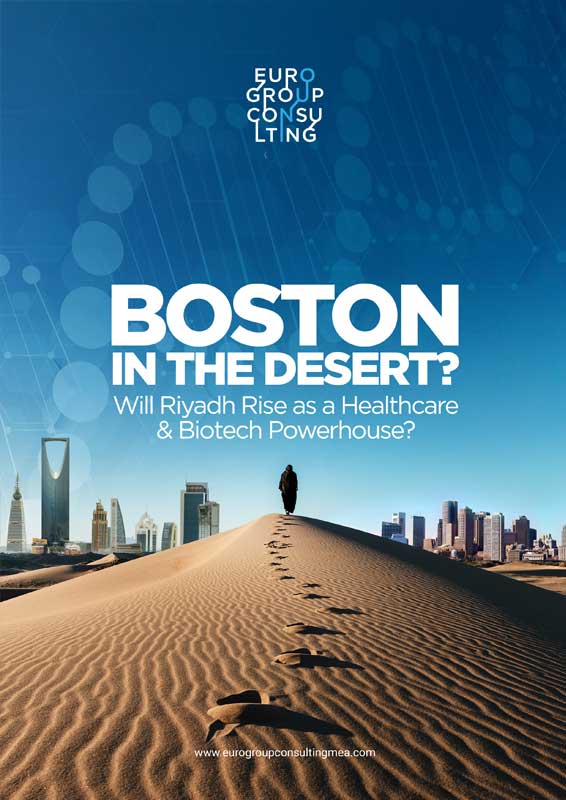
With the boom of Singapore’s construction sector, so does the rising costs. Construction costs are expected to increase by 5-6% in FY 2025 and 5-7% in FY 2026, driven by high material, labor, and equipment expenses. With total construction demand reaching S$44.2 billion in 2024, companies must find ways to cut costs while staying competitive. To navigate the challenges of Singapore Construction Cost Optimization, industry players are turning to technology and material efficiency. These strategies not only help control costs but also improve sustainability and productivity.
Singapore Construction Cost Optimization: Using Technology to Reduce Costs
One of the most effective ways to achieve Singapore construction cost optimization is through technological adoption. Advanced building methods like Building Information Modeling (BIM), prefabrication, and automation can improve efficiency, reduce waste, and lower labor costs.
For example, BIM helps construction firms plan projects more accurately, reducing errors and rework. Prefabrication allows parts of buildings to be manufactured off-site, cutting construction time and minimizing delays. Automation in tasks like bricklaying and welding can further save labor costs, which is crucial as wages continue to rise.
Material Efficiency: A Key to Singapore Construction Cost Optimization
With construction cost inflation averaging 3.8% across the Asia Pacific, finding ways to use materials efficiently is essential. Singapore’s industry is increasingly focusing on sustainable materials, alternative building components, and efficient supply chains.
By optimizing material usage and reducing waste, companies can offset rising costs. For instance, using high-performance concrete and recycled materials lowers material costs without compromising quality. Digital supply chain management also ensures that materials are ordered and used precisely, preventing over-purchasing and reducing waste.
Read Also The Power of Singapore Smart Building Technologies
Navigating Market Demand and Rising Costs
Despite cost pressures, Singapore’s construction market remains strong, driven by public institutional projects and public housing developments. This S$44.2 billion demand presents growth opportunities, but only for firms that manage their costs effectively.
Firms that adopt cost-efficient strategies—such as design standardization (used in HDB’s Prefab 2.0 initiative) and lean construction techniques—are better positioned to secure contracts. For example, Woh Hup’s use of Just-in-Time (JIT) delivery for materials has reduced storage costs and improved cash flow.
With continued government investment in infrastructure, firms that adopt cost-efficient strategies will be in a better position to secure contracts and remain profitable.
Comparing Singapore’s Costs to Regional Trends
While Asia Pacific faces an average 3.8% construction cost inflation, Singapore’s expenses are rising faster due to high labor costs, land scarcity, and strict sustainability regulations. However, proactive measures—such as cross-laminated timber (CLT) adoption (which is 20% cheaper than steel for mid-rise buildings) and off-site manufacturing—help local firms stay competitive.
For instance, China’s use of modular construction has kept costs low, while Australia’s focus on green building certifications has improved efficiency. Singapore can draw lessons from these markets while leveraging its strong digital infrastructure and government support to maintain its edge.
Read Also Is Digital Surveillance in China a High-Tech Dystopia?
Conclusion: The Future of Singapore Construction Cost Optimization
The rising costs in Singapore’s construction sector require proactive solutions. By embracing technology and optimizing material use, firms can stay profitable and meet the high market demand. As the nation’s infrastructure projects continue to grow, Singapore Construction Cost Optimization will be the key to success in the evolving construction landscape.
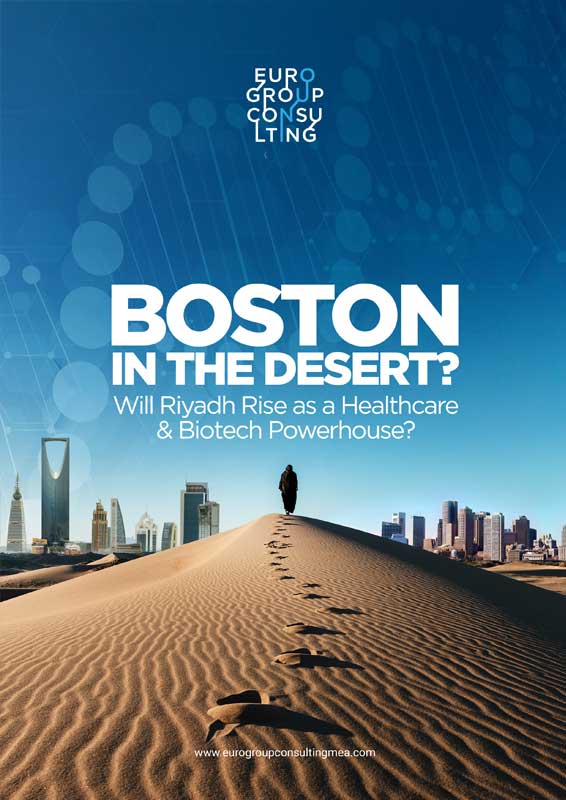